Як апрацоўваюцца высокадакладныя дэталі
2023-09-22
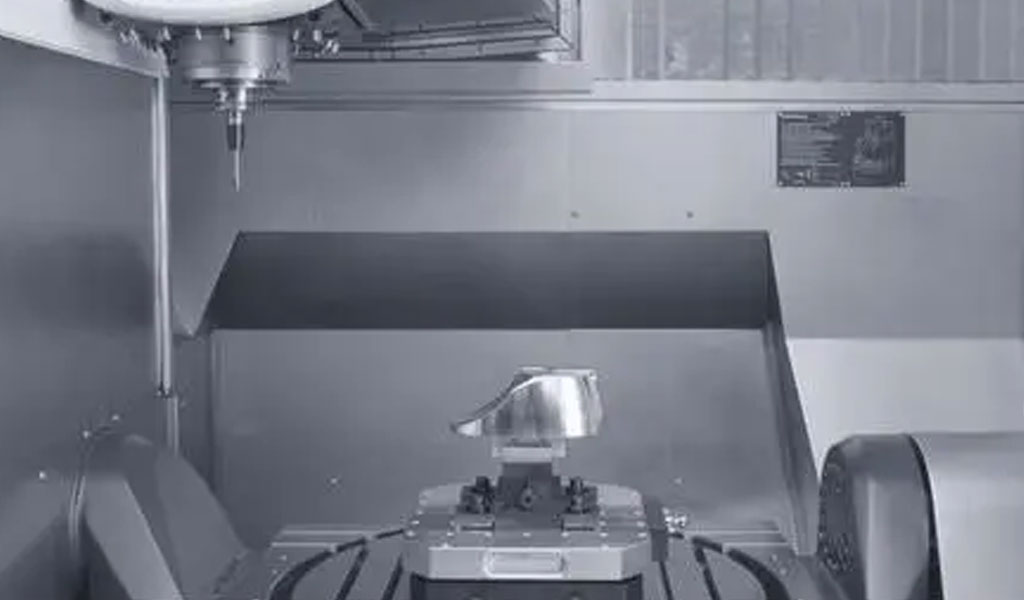
Разуменне дакладнай апрацоўкі
Дакладная апрацоўка з'яўляецца краевугольным каменем сучаснай вытворчасці, якая адказвае за вытворчасць складаных і дакладных кампанентаў, якія выкарыстоўваюцца ў розных галінах прамысловасці. Каб у поўнай меры зразумець яго значэнне, давайце вывучым асноўныя канцэпцыі дакладнай апрацоўкі, яе жыццёва важную ролю ў розных сектарах і гістарычны шлях, які прывёў да цяперашняга ўзроўню дасканаласці.А. Што такое прэцызійная апрацоўка?
Дакладная апрацоўка адносіцца да набору вытворчых працэсаў, якія выдаляюць матэрыял з нарыхтоўкі з высокай ступенню дакладнасці і кантролю, у выніку чаго атрымліваюцца тонка апрацаваныя кампаненты з жорсткімі допускамі. Гэты працэс ператварае сыравіну, такую як металы, пластмасы або кераміка, у дакладныя дэталі, якія адпавядаюць строгім патрабаванням. Асноўныя характарыстыкі дакладнай апрацоўкі ўключаюць:- Дакладнасць: Дакладная апрацоўка гарантуе, што канчатковы прадукт дакладна адпавядае задуманаму дызайну з мінімальнымі адхіленнямі.
- Жорсткія допускі: Гэта дазваляе вырабляць дэталі з надзвычай жорсткімі допускамі, што азначае, што гатовыя кампаненты дакладна адпавядаюць зададзеным вымярэнням.
- Палепшаная аздабленне паверхні: Дакладная апрацоўка забяспечвае выключную аздабленне паверхні, часта пазбаўляючы ад неабходнасці дадатковых працэсаў аздаблення.
- Комплексныя геаметрыі: Ён можа ствараць складаныя формы, контуры і асаблівасці, што робіць яго незаменным пры вытворчасці кампанентаў складанай канструкцыі.
- Паўтаранасць: Дакладнасць працэс апрацоўкіяны вельмі паўтараюцца, забяспечваючы нязменную якасць розных частак.
- Гнуткасць: Ён можа прымяняцца да шырокага спектру матэрыялаў, што робіць яго прыдатным для розных галін прамысловасці.
B. Важнасць дакладнай апрацоўкі
Дакладная апрацоўка мае велізарнае значэнне ў некалькіх важных галінах прамысловасці, уплываючы на розныя аспекты нашага паўсядзённага жыцця. Вось некалькі пераканаўчых прычын яго важнасці:- Аэракасмічная прамысловасць: У аэракасмічным сектары дакладная апрацоўка з'яўляецца незаменнай для вырабу кампанентаў, якія вытрымліваюць экстрэмальныя ўмовы. Авіярухавікі, пасадка перадача, а канструктыўныя элементы абапіраюцца на дэталі з дакладнай механічнай апрацоўкай для бяспекі і прадукцыйнасці.
- Медыцынскія прыборы: Такія медыцынскія прылады, як хірургічныя інструменты, пратэзы і імплантаваныя прылады, патрабуюць дакладнай апрацоўкі для забеспячэння біясумяшчальнасці, дакладнасці і бяспекі пацыентаў.
- Аўтамабільны сектар: Дэталі з дакладнай механічнай апрацоўкай неабходныя для аўтамабільнай прамысловасці для забеспячэння надзейнасці і эфектыўнасці аўтамабіляў. Такія кампаненты, як дэталі рухавіка, трансмісійныя сістэмы і тармазныя механізмы, залежаць ад дакладнай механічнай апрацоўкі.
- Электроніка і паўправаднікі: Дакладная механічная апрацоўка з'яўляецца ключавой у вытворчасці мікраэлектронных кампанентаў і паўправадніковых прыбораў, дзе мінімальныя допускі з'яўляюцца абавязковымі для функцыянальнасці.
- Энергетычны сектар: Энергетычная прамысловасць абапіраецца на прэцызійную механічную апрацоўку для вытворчасці важных частак, якія выкарыстоўваюцца ў вытворчасці электраэнергіі, у тым ліку турбін, генератараў і кампанентаў трансмісіі.
- Выраб інструментаў і штампаў: Дакладная апрацоўка мае вырашальнае значэнне ў вытворчасці інструментаў і штампаў, якія, у сваю чаргу, выкарыстоўваюцца для стварэння незлічонай колькасці іншых прадуктаў.
- Бытавая электроніка: Вытворчасць смартфонаў, наўтбукаў і іншай спажывецкай электронікі атрымлівае перавагі ад дакладнай апрацоўкі для забеспячэння элегантнага дызайну і аптымальнай функцыянальнасці.
- Даследаванні і распрацоўкі: Даследчыкі і навукоўцы залежаць ад высокадакладных кампанентаў для эксперыментаў, прататыпаў і лабараторнага абсталявання.
C. Гістарычная перспектыва
Падарожжа дакладнай механічнай апрацоўкі бярэ свой пачатак са старажытных цывілізацый, дзе ўмелыя рамеснікі выкарыстоўвалі элементарныя прылады для фарміравання матэрыялаў. Аднак дакладнасць, дасягнутая ў тыя часы, была абмежаванай у параўнанні з сучаснымі стандартамі.- Ранняя дакладная апрацоўка: Прамысловая рэвалюцыя 18-га і 19-га стагоддзяў адзначыла паваротны перыяд у развіцці дакладнай апрацоўкі. Вынаходніцтва станкоў, такіх як такарныя і фрэзерныя станкі, зрабіла рэвалюцыю ў вытворчасці, забяспечыўшы большую дакладнасць і паслядоўнасць.
- Другая сусветная вайна: Дакладная механічная апрацоўка адыграла ключавую ролю ў Другой сусветнай вайне, паколькі яна мела важнае значэнне для вытворчасці ваеннага абсталявання з неабходнай дакладнасцю і аднастайнасцю. Гэтая эпоха стала сведкам прагрэсу ў тэхніцы апрацоўкі і з'яўлення новых матэрыялаў.
- Пасляваенныя поспехі: У пасляваенны перыяд назіраўся ўсплёск тэхналагічных інавацый, у тым ліку выкарыстанне станкоў з лікавым праграмным кіраваннем (ЧПУ). ЧПУ дазволілі аўтаматызаваныя і высокадакладныя аперацыі, адкрываючы новую эру вытворчасці.
- Лічбавая эра: Інтэграцыя кампутараў і праграмнага забеспячэння ў працэсы апрацоўкі яшчэ больш павысіла дакладнасць апрацоўкі. Сучасныя станкі з ЧПУ могуць выконваць складаныя аперацыі з беспрэцэдэнтнай дакладнасцю, што робіць іх незаменнымі ў сучасным вытворчым ландшафце.
Матэрыялы і іх значэнне
Матэрыялы з'яўляюцца асновай дакладнай апрацоўкі, і выбар правільнага матэрыялу адыгрывае ключавую ролю ў вытворчасці высокадакладных дэталяў. У гэтым раздзеле мы паглыбімся ў важнасць выбару адпаведных матэрыялаў, зразумеем значэнне ўласцівасцей матэрыялу і вывучым розныя фактары, якія ўплываюць на апрацоўваемасць.А. Падбор матэрыялаў
Выбар матэрыялаў для дакладнай апрацоўкі з'яўляецца найважнейшым рашэннем, якое непасрэдна ўплывае на прадукцыйнасць, даўгавечнасць і функцыянальнасць канчатковага прадукту. Пры выбары матэрыялаў вытворцы павінны ўлічваць некалькі фактараў:- Прыдатнасць матэрыялу: Матэрыял павінен адпавядаць меркаванаму прымяненню. Розныя галіны прамысловасці і прымянення маюць розныя патрабаванні, такія як тэрмаўстойлівасць, устойлівасць да карозіі і электраправоднасць.
- механічныя ўласцівасці: Механічныя ўласцівасці, такія як трываласць на разрыў, цвёрдасць і пластычнасць, маюць вырашальнае значэнне. Напрыклад, у аэракасмічнай галіне матэрыялы з высокай трываласцю на разрыў аддаюць перавагу для канструктыўных кампанентаў.
- Цеплавыя ўласцівасці: Некаторыя прымянення патрабуюць матэрыялаў з выдатнай цеплаправоднасцю або ўстойлівасцю да высокіх тэмператур. Гэта асабліва важна ў такіх галінах, як энергетыка і электроніка.
- Устойлівасць да карозіі: У асяроддзях, дзе карозія выклікае занепакоенасць, перавага аддаецца матэрыялам з высокай устойлівасцю да карозіі, такім як нержавеючая сталь або тытан.
- Меркаванні вагі: Такія галіны прамысловасці, як аўтамабільная і аэракасмічная, часта аддаюць перавагу лёгкім матэрыялам, такім як алюміній або кампазіт з вугляроднага валакна, каб паменшыць расход паліва і павысіць прадукцыйнасць.
- Абмежаванні выдаткаў: Кошт з'яўляецца важным фактарам пры выбары матэрыялу. Высокапрадукцыйныя матэрыялы могуць быць дарагімі, таму вытворцы павінны знайсці баланс паміж прадукцыйнасцю і эканамічнасцю.
- Адпаведнасць нарматыўным патрабаванням: У такіх галінах, як ахова здароўя, матэрыялы павінны адпавядаць строгім нарматыўным стандартам біясумяшчальнасці і бяспекі.
- Наяўнасць: Наяўнасць матэрыялаў і іх крыніцы таксама ўплываюць на выбар. Некаторыя спецыялізаваныя сплавы або кампазіты могуць быць абмежаваныя.
B. Уласцівасці матэрыялу
Разуменне ўласцівасцей матэрыялаў мае вырашальнае значэнне для дакладнай апрацоўкі. Вось некаторыя ключавыя ўласцівасці матэрыялу і іх значэнне:- Трываласць на разрыў: Трываласць на разрыў вымярае здольнасць матэрыялу супрацьстаяць сіле нацягвання без разрыву. Гэта важна для структурных кампанентаў і дэталяў, якія падвяргаюцца механічным нагрузкам.
- Цвёрдасць: Цвёрдасць паказвае ўстойлівасць матэрыялу да дэфармацыі і зносу. Цвёрдыя матэрыялы падыходзяць для рэжучых інструментаў, у той час як больш мяккія матэрыялы могуць быць пераважнымі для некаторых прыкладанняў, напрыклад, ушчыльненняў.
- цягучасьць: Пластычнасць адносіцца да здольнасці матэрыялу дэфармавацца без разбурэння пры ўздзеянні на расцяжэнне. Плаўкія матэрыялы лягчэй фармаваць, але яны могуць быць непрыдатнымі для прымянення, дзе патрабуецца цвёрдасць.
- Цеплаправоднасць: Матэрыялы з высокай цеплаправоднасцю эфектыўна рассейваюць цяпло. Гэта ўласцівасць мае жыццёва важнае значэнне ў прыкладаннях, дзе кантроль тэмпературы мае вырашальнае значэнне.
- Электрычная праводнасць: Электраправоднасць важная ў электроніцы і электрычных кампанентах, дзе матэрыялы павінны спрыяць праходжанню электрычнасці.
- Магнітныя ўласцівасці: Магнітныя ўласцівасці важныя ў такіх галінах, як электрамагнітная і электроніка, дзе матэрыялы могуць быць ферамагнітнымі або немагнітнымі.
- хімічная ўстойлівасць: Матэрыялы павінны супрацьстаяць хімічнай карозіі ў асяроддзях, дзе яны падвяргаюцца ўздзеянню кіслот, шчолачаў або іншых агрэсіўных рэчываў.
C. Фактары апрацоўваемасці
Апрацоўвальнасць адносіцца да лёгкасці, з якой матэрыял можа быць апрацаваны, выразаны або сфармаваны. На гэта ўплываюць розныя фактары, у тым ліку:- Цвёрдасць матэрыялу: Мяккія матэрыялы, як правіла, лягчэй апрацоўваць, у той час як больш цвёрдыя матэрыялы могуць запатрабаваць спецыяльных інструментаў і метадаў.
- Фарміраванне сколаў: Утварэнне і выдаленне стружкі падчас механічнай апрацоўкі ўплывае на эфектыўнасць працэсу і якасць паверхні.
- Знос інструмента: Розныя матэрыялы могуць выклікаць розную ступень зносу інструмента, уплываючы на хуткасць апрацоўкі і кошт.
- Астуджальная вадкасць і змазка: Правільная астуджальная вадкасць і змазка неабходныя для памяншэння трэння, цяпла і зносу інструмента падчас апрацоўкі.
- хуткасць рэзання: Хуткасць, з якой рэжучы інструмент рухаецца праз матэрыял, уплывае як на прадукцыйнасць, так і на якасць апрацаванай паверхні.
- Інструментальны матэрыял: Выбар матэрыялу рэжучага інструмента, напрыклад, цвёрдасплаўнай або хуткарэзнай сталі, залежыць ад матэрыялу, які апрацоўваецца.
- Параметры рэзкі: Рэгуляванне такіх параметраў рэзкі, як хуткасць падачы і глыбіня рэзання, можа аптымізаваць працэс апрацоўкі пэўных матэрыялаў.
Станкі для дакладнай апрацоўкі
Станкі з'яўляюцца сэрцам дакладнай апрацоўкі, што дазваляе пераўтвараць сыравіну ў дэталі высокай дакладнасці. У гэтым раздзеле мы разгледзім чатыры асноўныя тыпы станкоў, якія выкарыстоўваюцца ў дакладнай апрацоўцы: апрацоўчыя цэнтры з ЧПУ, такарныя станкі, шліфавальныя станкі і EDM (электраэрозная апрацоўка). Кожная з гэтых машын адыгрывае ўнікальную ролю ў вытворчасці дакладных кампанентаў.А. Апрацоўчыя цэнтры з ЧПУ
Апрацоўчыя цэнтры з ЧПУ (кампутарным лікавым кіраваннем) з'яўляюцца універсальнымі і шырока выкарыстоўваюцца ў дакладнай апрацоўцы. Гэта аўтаматызаваныя сістэмы, якія кантралююць рух рэжучых інструментаў і нарыхтовак з выключнай дакладнасцю. Вось агляд апрацоўваючых цэнтраў з ЧПУ і іх значэнне:- Гнуткасць: Апрацоўчыя цэнтры з ЧПУ могуць выконваць розныя апрацоўчыя аперацыі, у тым ліку фрэзераванне, свідраванне і наразанне метчыкаў. Гэтая ўніверсальнасць дазваляе вырабляць складаныя дэталі з мноствам функцый.
- Высокая дакладнасць: Камп'ютэрызаванае кіраванне станкамі з ЧПУ забяспечвае дакладнае размяшчэнне інструмента і стабільныя вынікі, што робіць іх ідэальнымі для дэталяў з жорсткімі допускамі.
- Аўтаматызацыя: Апрацоўчыя цэнтры з ЧПУ могуць працаваць бесперапынна з мінімальным умяшаннем чалавека. Гэтая аўтаматызацыя павышае эфектыўнасць і зніжае рызыку памылак.
- Комплексныя геаметрыі: Яны выдатныя ў апрацоўцы складаных формаў і контураў, што робіць іх прыдатнымі для такіх галін, як аэракасмічная прамысловасць, дзе складаныя кампаненты з'яўляюцца звычайнай з'явай.
- Паўтаральныя вынікі: Станкі з ЧПУ забяспечваюць выдатную паўтаральнасць, гарантуючы, што кожная вырабленая дэталь дакладна адпавядае спецыфікацыям канструкцыі.
- Скарачэнне часу ўстаноўкі: Апрацоўчыя цэнтры з ЧПУ можна запраграмаваць на хуткае пераключэнне паміж рознымі задачамі, мінімізуючы час наладкі і павялічваючы эфектыўнасць вытворчасці.
B. Такарныя станкі
Такарныя станкі выкарыстоўваюцца для стварэння цыліндрычных дэталяў шляхам кручэння нарыхтоўкі, у той час як рэжучы інструмент здымае матэрыял з яе вонкавай паверхні. Яны неабходныя для вытворчасці валs, шпількі і іншыя кампаненты з вярчальнай сіметрыяй. Асноўныя моманты аб такарных станках ўключаюць:- Цыліндрычныя дэталі: Такарныя станкі спецыялізуюцца на вытворчасці цыліндрычных або трубчастых дэталяў, у тым ліку з разьбой або мудрагелістымі канаўкамі.
- Высокія хуткасці: Яны працуюць на высокіх хуткасцях, што робіць іх прыдатнымі для дэталяў, якія патрабуюць гладкай і дакладнай аздаблення.
- Аперацыя па адной восі: Большасць такарных станкоў з'яўляюцца аднавосевымі, арыентаванымі на фарміраванне вонкавай паверхні загатоўкі.
- Эфектыўны для масавай вытворчасці: Такарная апрацоўка вельмі эфектыўная для масавай вытворчасці дэталяў з мінімальнымі адходамі.
- Такарныя станкі: Такарныя станкі з ручным кіраваннем і ЧПУ - гэта звычайна выкарыстоўваюцца такарныя станкі, якія прапануюць шэраг магчымасцей.
C. Шліфавальныя станкі
Шліфавальныя станкі прызначаны для дакладнай апрацоўкі паверхні і фарміравання цвёрдых або абразіўных матэрыялаў. Яны маюць вырашальнае значэнне для дасягнення вельмі жорсткіх допускаў і найвышэйшай аздаблення паверхні. Вось чаму шліфавальныя машыны важныя:- Дакладнасць мікроннага ўзроўню: Шліфавальныя машыны могуць дасягаць дакладнасці да мікрон, што робіць іх неабходнымі для прыкладанняў, якія патрабуюць найвышэйшага ўзроўню дакладнасці.
- Выдаленне матэрыялу: Яны выдаляюць матэрыял шляхам ізаляцыі, дазваляючы выправіць недахопы паверхні і дасягнуць выключнай гладкасці.
- Заточка інструментаў і фрэз: У дадатак да шліфавання паверхні існуюць спецыялізаваныя шліфавальныя станкі для завострывання рэжучых інструментаў і атрымання дакладных профіляў.
- Разнастайнасць спосабаў драбнення: Розныя тыпы шліфавальных машын, у тым ліку плоскашліфавальныя машыны, цыліндрычныя шліфавальныя машыны і бесцэнтравыя шліфавальныя машыны, задавальняюць розныя патрэбы апрацоўкі.
- Загартаваныя матэрыялы: Шліфаванне асабліва падыходзіць для загартаваных матэрыялаў, такіх як інструментальная сталь і кераміка, дзе традыцыйныя метады апрацоўкі могуць быць неэфектыўнымі.
D. EDM (электрычная апрацоўка)
Электраэрозійная апрацоўка - гэта нетрадыцыйны працэс апрацоўкі, які выкарыстоўвае электрычныя разрады для фарміравання матэрыялаў. Ён ідэальна падыходзіць для стварэння складаных і далікатных дэталяў, дзе традыцыйныя рэжучыя інструменты могуць пашкодзіць. Ключавыя аспекты EDM ўключаюць:- Няма фізічнага кантакту: EDM не прадугледжвае прамога фізічнага кантакту паміж інструментам і нарыхтоўкай, мінімізуючы рызыку зносу інструмента і пашкоджання далікатных матэрыялаў.
- Высокая дакладнасць: Ён можа дасягнуць высокай дакладнасці і якасці аздаблення паверхні, нават з выключна цвёрдымі матэрыяламі.
- Электраэрозія дроту і грузіла: Ёсць два асноўных тыпу машын EDM: рэзка дроту EDM, які выкарыстоўвае драцяны электрод, і грузіла EDM, які выкарыстоўвае фасонны электрод.
- Складаныя формы: EDM можа вырабляць складаныя формы, такія як штампы і прэс-формы, са складанымі дэталямі і дробнымі рысамі.
- Зона цеплавога ўздзеяння: Паколькі EDM не выдзяляе цяпло ў нарыхтоўцы, ён падыходзіць для адчувальных да цяпла матэрыялаў, такіх як аэракасмічныя сплавы.
- Павольны працэс: Электраэрозія адносна павольная ў параўнанні з іншымі метадамі апрацоўкі, што робіць яе найбольш прыдатнай для невялікай колькасці высокадакладных работ.
Рэжучыя інструменты і аснастка
Рэжучыя інструменты знаходзяцца ў авангардзе дакладнай апрацоўкі, служачы інструментамі, якія фармуюць і ператвараюць сыравіну ў дэталі высокай дакладнасці. У гэтым раздзеле мы вывучым розныя тыпы рэжучых інструментаў, важнасць пакрыцця інструментаў і фактары, якія ўплываюць на тэрмін службы і знос інструментаў.А. Віды рэжучых інструментаў
Дакладная апрацоўка абапіраецца на разнастайны спектр рэжучых інструментаў, кожны з якіх прызначаны для канкрэтных задач і матэрыялаў. Выбар рэжучага інструмента ў значнай ступені ўплывае на эфектыўнасць і дакладнасць працэсу апрацоўкі. Вось некалькі распаўсюджаных тыпаў рэжучых інструментаў:- Канцавыя фрэзы: Канцавыя фрэзы - гэта ўніверсальныя інструменты, якія выкарыстоўваюцца для фрэзеравання. Яны маюць некалькі рэжучых беражкоў і могуць выдаляць матэрыял з нарыхтоўкі рознымі спосабамі, у тым ліку абліцоўваннем, контурам і прарэзам.
- Свердзела: Свердзелы прызначаны для стварэння адтулін у дэталях. Яны бываюць розных формаў, у тым ліку спіральныя свердзелы, цэнтральныя свердзелы і зменныя свердзелы.
- Такарныя ўстаўкі: Яны выкарыстоўваюцца ў такарных станках для фарміравання цыліндрычных дэталяў. Такарныя ўстаўкі даступныя ў розных формах і матэрыялах, якія падыходзяць для розных прыкладанняў.
- Фрэзы: Фрэзы бываюць розных формаў, напрыклад, тарцовыя фрэзы, шаравыя млыны і фрэзы для пазаў, і выкарыстоўваюцца ў фрэзерных станках для стварэння розных элементаў на нарыхтоўцы.
- Разгорткі: Разгорткі выкарыстоўваюцца для аздаблення і падбору памераў раней прасвідраваных адтулін да дакладных памераў. Яны забяспечваюць гладкія і дакладныя паверхні адтулін.
- Краны і памірае: Гэтыя рэжучыя інструменты выкарыстоўваюцца для наразання разьбы. Метчыкі ствараюць унутраную разьбу, а плашчакі - знешнюю.
- шлифкругов: Шліфавальныя кругі - гэта абразіўныя інструменты, якія выкарыстоўваюцца для дакладнага шліфавання паверхні. Яны даступныя з розных абразіўных матэрыялаў і памераў зярністасці.
- Брошкі: Працяжкі - гэта спецыяльныя інструменты, якія выкарыстоўваюцца для выразання ўнутраных і знешніх формаў і профіляў, такіх як шпонкавыя канаўкі і шпонкі.
- Зенкеры і зенкеры: Гэтыя інструменты выкарыстоўваюцца для стварэння паглыбленняў або фаскі вакол адтулін для зашпількаs.
- Сумныя бары: Свідравальныя брускі выкарыстоўваюцца ў свідравальных аперацыях для пашырэння існуючых адтулін з дакладнасцю.
Б. Пакрыцці для інструментаў
Пакрыцці інструментаў - гэта тонкія пласты матэрыялу, якія наносяцца на рэжучыя інструменты для павышэння іх прадукцыйнасці і даўгавечнасці. Гэтыя пакрыцця маюць некалькі пераваг:- Зніжэнне трэння: Пакрыцці, такія як нітрыд тытана (TiN) і карбанітрыд тытана (TiCN), памяншаюць трэнне паміж інструментам і нарыхтоўкай, што прыводзіць да больш гладкага рэзання і больш працяглага тэрміну службы інструмента.
- Палепшаная цвёрдасць: Пакрыцці павялічваюць цвёрдасць паверхні інструмента, робячы яго больш устойлівым да зносу і падаўжаючы тэрмін службы інструмента.
- Палепшаная тэрмаўстойлівасць: Пакрыцці вытрымліваюць высокія тэмпературы, якія ўзнікаюць падчас механічнай апрацоўкі, памяншаючы звязаны з цяплом знос інструмента і павялічваючы хуткасць рэзання.
- Уласцівасці супраць назапашвання: Некаторыя пакрыцця валодаюць антыадгезійнымі ўласцівасцямі, прадухіляючы назапашванне матэрыялу на рэжучых беражках інструмента.
- Падвышаная змазачная здольнасць: Інструменты з пакрыццём валодаюць палепшанай змазачнай здольнасцю, памяншаючы патрэбу ў празмернай колькасці астуджальнай вадкасці і паляпшаючы адвод стружкі.
C. Тэрмін службы і знос інструмента
Разуменне тэрміну службы і зносу інструмента мае вырашальнае значэнне для аптымізацыі працэсаў апрацоўкі і мінімізацыі вытворчых выдаткаў. Тэрмін службы інструмента - гэта час, на працягу якога рэжучы інструмент застаецца эфектыўным, перш чым спатрэбіцца яго замена або аднаўленне. Некалькі фактараў уплываюць на тэрмін службы і знос інструмента:- хуткасць рэзання: Больш высокія хуткасці рэзання могуць прывесці да павышанага зносу інструмента з-за больш высокіх тэмператур, якія ўзнікаюць падчас апрацоўкі. Правільны выбар хуткасцей рэзкі мае важнае значэнне для збалансавання тэрміну службы інструмента і прадукцыйнасці.
- хуткасць падачы: Хуткасць, з якой рэжучы інструмент прасоўваецца ў нарыхтоўку, уплывае на знос інструмента. Высокая падача можа паскорыць знос, у той час як меншая падача можа падоўжыць тэрмін службы інструмента.
- Глыбіня рэзу: Глыбіня рэзання ўплывае на колькасць выдаленага матэрыялу за праход. Больш глыбокія парэзы могуць павялічыць знос інструмента, таму аптымізацыя глыбіні мае вырашальнае значэнне.
- Цвёрдасць матэрыялу: Рэзка цвёрдых матэрыялаў можа паскорыць знос інструмента. Спецыялізаваныя інструменты і пакрыцця выкарыстоўваюцца для эфектыўнай апрацоўкі цвёрдых матэрыялаў.
- Астуджальная вадкасць і змазка: Належная астуджальная вадкасць і змазка дапамагаюць рассейваць цяпло і памяншаць трэнне, падаўжаючы тэрмін службы інструмента.
- Інструментальны матэрыял: Матэрыял, з якога выраблены рэжучы інструмент, уплывае на яго зносаўстойлівасць. Такія матэрыялы, як карбід і кераміка, забяспечваюць выдатную зносаўстойлівасць.
- Геаметрыя інструмента: Геаметрыя рэжучага інструмента, у тым ліку перад вуглом, рэльефным вуглом і канструкцыяй стружколома, адыгрывае значную ролю ў характары зносу.
- Матэрыял нарыхтоўкі: Тып матэрыялу, які апрацоўваецца, уплывае на знос інструмента. Абразіўныя матэрыялы могуць прывесці да больш хуткага зносу інструмента.
Працэсы дакладнай апрацоўкі
Працэсы прэцызійнай апрацоўкі - гэта метады, з дапамогай якіх сыравіна ператвараецца ў дэталі высокай дакладнасці з жорсткімі допускамі і выключнай аздабленнем паверхні. У гэтым раздзеле мы разгледзім пяць ключавых працэсаў дакладнай апрацоўкі: такарная апрацоўка, фрэзераванне, свідраванне, шліфаванне і электраэрозійная апрацоўка (EDM). Кожны з гэтых працэсаў служыць унікальнай мэты і выкарыстоўваецца ў залежнасці ад канкрэтных патрабаванняў да дэталі.А. Паварот
Такарная апрацоўка - гэта працэс апрацоўкі, які ў асноўным выкарыстоўваецца для фарміравання цыліндрычных дэталяў. Гэта ўключае ў сябе кручэнне нарыхтоўкі, у той час як аднакропкавы рэжучы інструмент выдаляе матэрыял з вонкавай паверхні. Вось асноўныя аспекты павароту:- Цыліндрычныя дэталі: Такарная апрацоўка ідэальна падыходзіць для вытворчасці цыліндрычных кампанентаў, такіх як валы, шпількі і ўтулкі.
- Круцільная сіметрыя: Ён добра падыходзіць для дэталяў, якія патрабуюць круцільнай сіметрыі, паколькі нарыхтоўка круціцца на такарным станку, а рэжучы інструмент фарміруе яе.
- Розныя аперацыі: Такарная апрацоўка можа выконваць розныя аперацыі, у тым ліку абліцоўванне, абточванне (памяншэнне дыяметра), абточванне кануса і наразанне разьбы.
- Рэзка ў адну кропку: Адзін рэжучы інструмент выдаляе матэрыял бесперапынным рухам, што прыводзіць да эфектыўнага выдалення матэрыялу.
- Такарныя станкі: Такарныя станкі з ручным і кіраваным ЧПУ звычайна выкарыстоўваюцца для такарных аперацый.
Б. Фрэзераванне
Фрэзераванне - гэта універсальны працэс дакладнай апрацоўкі, які выкарыстоўвае шматкропкавыя рэжучыя інструменты для выдалення матэрыялу з нарыхтоўкі. Ён добра падыходзіць для стварэння шырокага спектру формаў і функцый. Ключавыя аспекты фрэзеравання ўключаюць:- Гнуткасць: Фрэзераванне можа вырабляць плоскія паверхні, прарэзы, кішэні і складаныя контуры. Ён выкарыстоўваецца як для 2D, так і для 3D апрацоўкі.
- Шматкропкавая рэзка: Некалькі рэжучых беражкоў на інструменце ўзаемадзейнічаюць з нарыхтоўкай адначасова, што дазваляе эфектыўна здымаць матэрыял.
- Віды фрэзеравання: Фрэзераванне можна выконваць з дапамогай розных тыпаў фрэз, у тым ліку кантавых фрэз, тарцовых і шаравых млыноў.
- Апрацоўчыя цэнтры з ЧПУ: Фрэзерныя станкі з ЧПУ забяспечваюць дакладны кантроль за рухам інструмента і шырока выкарыстоўваюцца ў сучаснай апрацоўцы.
- Высокія хуткасці: Фрэзераванне можна выконваць на высокіх хуткасцях, што забяспечвае эфектыўную вытворчасць.
C. Свідраванне
Свідраванне - гэта дакладны працэс апрацоўкі, які выкарыстоўваецца для стварэння адтулін у нарыхтоўках. Гэта фундаментальная аперацыя ў розных галінах. Асноўныя аспекты свідравання ўключаюць:- Стварэнне дзіркі: Свідравальныя станкі выкарыстоўваюць спецыялізаваныя інструменты, якія называюцца свердзеламі, для выдалення матэрыялу і стварэння адтулін пэўнага дыяметра.
- Віды свердзелаў: Даступныя розныя тыпы свердзелаў, у тым ліку спіральныя, цэнтральныя і зменныя свердзелы, кожнае з якіх прызначана для канкрэтнага прымянення.
- Дакладнасць: Дакладнае пазіцыянаванне і выраўноўванне важныя пры свідраванні, каб адтуліны ствараліся з дакладнасцю.
- Хуткасць і хуткасць падачы: Такія параметры свідравання, як хуткасць кручэння і падача, маюць вырашальнае значэнне для дасягнення патрэбных памераў адтуліны.
- Астуджальная вадкасць і змазка: Належная астуджальная вадкасць і змазка выкарыстоўваюцца для рассейвання цяпла і памяншэння трэння падчас свідравання.
Д. Шліфаванне
Шліфаванне - гэта дакладны працэс апрацоўкі, які выкарыстоўвае абразіўныя кругі для выдалення матэрыялу і дасягнення вельмі жорсткіх допускаў і аздаблення паверхні. Асноўныя аспекты драбнення ўключаюць:- Выключная дакладнасць: Шліфаванне можа дасягнуць дакладнасці да мікрон, што робіць яго ідэальным для прыкладанняў, якія патрабуюць найвышэйшай дакладнасці.
- чысціня паверхні: Ён стварае цудоўную аздабленне паверхні, часта пазбаўляючы ад неабходнасці дадатковых працэсаў аздаблення.
- матэрыялы: Шліфаванне падыходзіць для цвёрдых і абразіўных матэрыялаў, уключаючы загартаваную сталь, кераміку і карбіды.
- Разнастайнасць спосабаў драбнення: Розныя тыпы шліфавальных машын, такіх як плоскашліфавальныя машыны, цыліндрычныя шліфавальныя машыны і бесцэнтравыя шліфавальныя машыны, задавальняюць розныя патрэбы апрацоўкі.
- Астуджальная вадкасць: Правільная астуджальная вадкасць важная пры шліфоўцы, каб прадухіліць перагрэў і захаваць цэласнасць колы.
E. Электрычная апрацоўка (EDM)
Электраразрадная апрацоўка - гэта нетрадыцыйны працэс дакладнай апрацоўкі, які выкарыстоўвае электрычныя разрады для выдалення матэрыялу. Ён асабліва падыходзіць для апрацоўкі складаных і складаных формаў, а таксама цвёрдых і тэрмаўстойлівых матэрыялаў. Ключавыя аспекты EDM ўключаюць:- Бескантактавая апрацоўка: EDM не прадугледжвае прамога кантакту паміж інструментам і нарыхтоўкай, што зніжае рызыку зносу і пашкоджання інструмента.
- Высокая дакладнасць: Электраразмеркаванне дазваляе дасягнуць высокай дакладнасці, што робіць яго прыдатным для прымянення, дзе важныя жорсткія допускі.
- Складаныя формы: Ён выдатны ў апрацоўцы складаных формаў, штампаў, прэс-формаў і кампанентаў з дробнымі дэталямі.
- Электраэрозія дроту і грузіла: Ёсць два асноўных тыпу машын EDM: дрот EDM, які выкарыстоўвае драцяны электрод, і грузіла EDM, які выкарыстоўвае фасонны электрод.
- Павольны працэс: Электраэрозія адносна павольная ў параўнанні з іншымі метадамі апрацоўкі, што робіць яе найбольш прыдатнай для невялікай колькасці высокадакладных работ.
Допускі і кантроль якасці
Дакладная апрацоўка патрабуе дбайнай увагі да дэталяў і строгага кантролю якасці, каб пераканацца, што дэталі адпавядаюць вызначаным стандартам. У гэтым раздзеле мы вывучым тры важныя аспекты кантролю якасці ў прэцызійнай апрацоўцы: геаметрычныя памеры і допускі (GD&T), статыстычны кантроль працэсу (SPC) і забеспячэнне якасці.A. Геаметрычныя памеры і допускі (GD&T)
Нанясенне геаметрычных памераў і допускаў, часта скарочана GD&T, - гэта сістэма, якая выкарыстоўваецца для вызначэння і перадачы дапушчальных варыяцый памеру, формы, арыентацыі і размяшчэння элементаў дэталі. GD&T мае жыццёва важнае значэнне для дакладнай апрацоўкі па наступных прычынах:- Дакладная камунікацыя: GD&T забяспечвае стандартызаваную мову для інжынераў, дызайнераў і машыністаў, каб дакладна перадаць задумы праектавання і патрабаванні да памераў.
- Удакладненне талерантнасці: Гэта дапамагае вызначыць дапушчальную варыяцыю ў крытычных памерах, гарантуючы, што ўсе зацікаўленыя бакі разумеюць дапушчальныя адхіленні.
- Палепшаная якасць: GD&T спрыяе павышэнню якасці за кошт памяншэння двухсэнсоўнасці ў спецыфікацыях праектавання, зводзячы да мінімуму рызыку памылак падчас апрацоўкі.
- Эканамічнасць: Выразныя спецыфікацыі GD&T могуць прывесці да зніжэння выдаткаў на вытворчасць, паколькі менш верагоднасць таго, што дэталі будуць утылізаваны або патрабуюць пераробкі з-за непаразумення або няправільнай інтэрпрэтацыі.
- Комплексная геаметрыя: Гэта асабліва карысна для дэталяў са складанай геаметрыяй, гарантуючы, што ўсе функцыі вырабляюцца ў адпаведнасці з патрэбнымі характарыстыкамі.
B. Статыстычны кантроль працэсу (SPC)
Статыстычны кантроль працэсу (SPC) - гэта метадалогія кантролю якасці, якая выкарыстоўвае статыстычныя метады для кантролю і кіравання працэсам апрацоўкі. SPC мае важнае значэнне ў прэцызійнай апрацоўцы па наступных прычынах:- Маніторынг працэсаў: SPC дапамагае кантраляваць працэсы апрацоўкі ў рэжыме рэальнага часу, выяўляючы варыяцыі або адхіленні ад патрэбных параметраў.
- Ранняе выяўленне праблем: Пастаянна кантралюючы працэс, SPC дазваляе ранняе выяўленне праблем, якія могуць прывесці да дэталяў, якія не адпавядаюць спецыфікацыям, памяншаючы адходы і перапрацоўку.
- Прыняцце рашэнняў на аснове дадзеных: SPC абапіраецца на дадзеныя і статыстычны аналіз для прыняцця абгрунтаваных рашэнняў аб карэкціроўцы працэсу, гарантуючы, што працэс апрацоўкі застаецца ў дапушчальных межах.
- Палепшаная кансістэнцыя: SPC спрыяе ўзгодненасці працэсу і зніжае верагоднасць вытворчасці неадпаведных дэталяў.
- Скарачэнне лому і перапрацоўкі: Аператыўна выяўляючы і вырашаючы змены ў працэсе, SPC мінімізуе вытворчасць дэфектных дэталяў, зніжаючы выдаткі на лом і пераробку.
C. Забеспячэнне якасці ў прэцызійнай апрацоўцы
Забеспячэнне якасці ў прэцызійнай апрацоўцы ахоплівае комплексны падыход да забеспячэння таго, каб вырабленыя дэталі адпавядалі вызначаным стандартам якасці або перавышалі іх. Яна ўключае ў сябе розныя элементы, у тым ліку:- Дакументацыя працэсу: Падрабязная дакументацыя працэсаў апрацоўкі, уключаючы стандартныя аперацыйныя працэдуры (SOP) і працоўныя інструкцыі, гарантуе паслядоўнае выкананне кожнага этапу.
- Кантроль і вымярэнне: Строгая праверка і вымярэнне з выкарыстаннем дакладных прыбораў і метадаў метралогіі правяраюць адпаведнасць дэталяў устаноўленым допускам і стандартам якасці.
- Каліброўка: Рэгулярная каліброўка апрацоўчага абсталявання і вымяральных прыбораў важная для падтрымання дакладнасці і прасочвальнасці.
- Праверка матэрыялу: Праверка ўласцівасцей, складу і якасці матэрыялу мае вырашальнае значэнне для таго, каб гарантаваць, што выкарыстоўваны матэрыял адпавядае праектным патрабаванням.
- Навучанне супрацоўнікаў: Праграмы навучання і павышэння кваліфікацыі для машыністаў і персаналу кантролю якасці гарантуюць, што яны валодаюць сваімі ролямі і абавязкамі.
- Аналіз асноўных прычын: Пры выяўленні частак, якія не адпавядаюць патрабаванням, праводзіцца аналіз першапрычын, каб вызначыць крыніцу праблемы і ўжыць меры па выпраўленні.
- Пастаяннае ўдасканаленне: Культура пастаяннага ўдасканалення спрыяе інавацыям і стымулюе пастаянныя ўдасканаленні працэсаў апрацоўкі і працэдур кантролю якасці.
- Зваротная сувязь з кліентам: Збор і аналіз водгукаў кліентаў дапамагае вызначыць вобласці для паляпшэння і ўзгадняе працэсы апрацоўкі з чаканнямі кліентаў.
заключэнне
А. Мастацтва і навука дакладнай апрацоўкі
Прэцызійная апрацоўка знаходзіцца на стыку мастацтва і навукі, дзе крэатыўнасць, навыкі і інавацыі збліжаюцца для вытворчасці высокадакладных дэталяў, якія рухаюць прамысловасць і фарміруюць сучасны свет. Гэта і форма мастацтва, якая патрабуе майстэрства і вопыту машыністаў, якія ператвараюць сыравіну ў творы інжынернай дасканаласці, і навука, якая абапіраецца на перадавыя тэхналогіі, матэрыялазнаўства і перадавыя працэсы для дасягнення беспрэцэдэнтнай дакладнасці. Падарожжа па дакладнай механічнай апрацоўцы вядзе нас праз разуменне матэрыялаў і іх уласцівасцей, валоданне рэжучымі інструментамі і механізмамі, а таксама дбайны кантроль працэсаў і допускаў. Ён ахоплівае мову нанясення геаметрычных памераў і допускаў, пільнасць статыстычнага кантролю працэсу і прыхільнасць забеспячэнню якасці. Дакладная апрацоўка адыгрывае ключавую ролю ў розных галінах прамысловасці, ад аэракасмічнай і аўтамабільнай да медыцынскіх прыбораў і электронікі, фарміруючы ўсё: ад авіяцыйных рухавікоў да штучных суставаў і мікрачыпаў. Гэта дазваляе ствараць кампаненты, якія працуюць з неперасягненай дакладнасцю і надзейнасцю, часта рассоўваючы межы магчымага.Б. Заключныя думкі
Калі мы завяршаем гэтае даследаванне дакладнай апрацоўкі, становіцца ясна, што гэта сфера не толькі аб стварэнні дэталяў; гаворка ідзе пра стварэнне магчымасцей. Імкненне да дакладнасці рухае інавацыі, рассоўваючы межы таго, чаго можна дасягнуць. Няхай гэта будзе тонкае майстэрства, неабходнае для стварэння мудрагелістых механізмаў гадзінніка, або перадавыя тэхналогіі, неабходныя для вытворчасці складаных аэракасмічных кампанентаў, дакладная апрацоўка ляжыць у аснове ўсяго гэтага. Будучыня дакладнай апрацоўкі шматабяцальная. Дасягненні ў галіне матэрыялазнаўства, аўтаматызацыі і лічбавых тэхналогій працягваюць змяняць ландшафт. Мініяцюрызацыя, 3D-друк і метады ўстойлівай вытворчасці становяцца ўсё больш прыкметнымі, адкрываючы новыя гарызонты для галіны. У свеце, дзе дакладнасць важная як ніколі, дакладная апрацоўка застаецца незаменнай асновай сучаснага машынабудавання. Гэта сведчанне чалавечай вынаходлівасці і нашага нязменнага імкнення да дасканаласці ва ўсіх аспектах вытворчасці. Па меры росту попыту на больш высокую дакладнасць і больш складаныя кампаненты, дакладная апрацоўка будзе працягваць развівацца, вырашаючы задачы заўтрашняга дня з такой жа адданасцю і дакладнасцю, якія вызначалі яе на працягу стагоддзяў.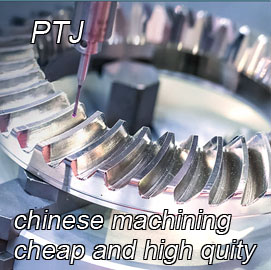
Нашы паслугі
- 5 Апрацоўка восі
- Фрэзераванне cnc
- Паварот cnc
- Апрацоўчая прамысловасць
- Працэс апрацоўкі
- Апрацоўка паверхняў
- Механічная апрацоўка металу
- Апрацоўка пластыка
- Парашковая металургія Цвіль
- Ліццё пад ціскам
- Галерэя запчастак
Прыклады
- Аўтазапчасткі для металу
- дэталяў машын
- Святлодыёдны радыятар
- Часткі будаўніцтва
- Мабільныя часткі
- Медыцынскія часткі
- Электронныя дэталі
- Індывідуальная апрацоўка
- часткі ровараў
Спіс матэрыялаў
- Апрацоўка алюмінія
- Апрацоўка тытана
- Механічная апрацоўка нержавеючай сталі
- Апрацоўка медзі
- Апрацоўка латуні
- Суперсплаўная апрацоўка
- Peek апрацоўка
- Апрацоўка UHMW
- Аднатонная апрацоўка
- PA6 Апрацоўка
- Апрацоўка PPS
- Апрацоўка тэфлонам
- Апрацоўка Інконеля
- Апрацоўка інструментальнай сталі
- Больш матэрыялу
Галерэя запчастак